Understanding Operational Efficiency in the Laundry Business
What Does Operational Efficiency Mean in a Laundry Context?
Operational efficiency in the laundry business refers to the ability to deliver high-quality laundry services while minimizing waste of time, resources, and costs. According to TechTarget, it balances the inputs like labor and equipment with outputs such as rapid turnaround times and customer satisfaction. In simpler terms, it’s about doing more with less—providing exemplary service while using fewer resources, thus enhancing profitability.
In the context of laundry operations, this involves a variety of factors including effective machine usage, optimized workflow processes, and streamlined scheduling of tasks. By focusing on operational efficiency, laundry businesses can reduce errors, increase cleanliness, and ultimately, elevate customer satisfaction.
How Can You Measure Efficiency in Laundry Operations?
Measuring efficiency in laundry operations involves several key performance indicators (KPIs). Common metrics include:
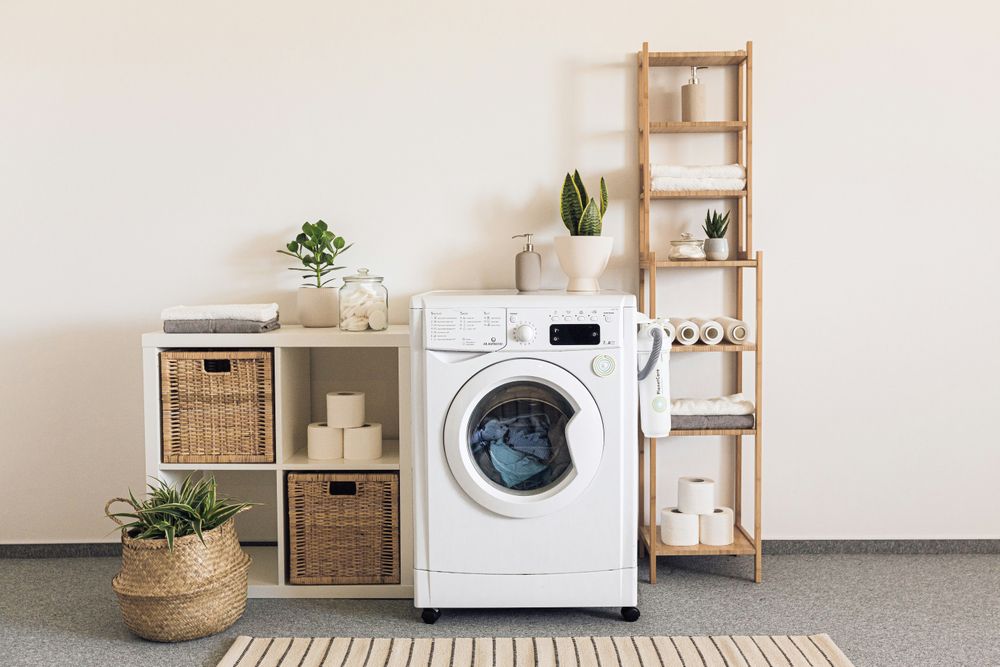
Measuring efficiency in laundry operations involves several key performance indicators (KPIs) such as turnaround time, equipment utilization, resource consumption, and quality control. Implementing these metrics enables owners to gather quantitative data and make informed decisions.
Turnaround Time: This is the time taken from receiving a customer's laundry to returning it. Shorter turnaround times often lead to higher customer satisfaction.
Equipment Utilization: Monitoring how effectively machines are used helps in understanding whether more equipment is needed or if existing equipment can handle peak loads more efficiently.
Resource Consumption: Tracking water and energy usage can uncover areas for costing improvement, leading to reduced operational costs. Technologies like those mentioned in Precision Appliance Leasing can help monitor these metrics in real-time.
Quality Control: Regular inspections and adherence to quality standards ensure that the laundry service remains consistent and meets customer expectations.
Implementing these metrics allows owners to gather quantitative data on their operations, ultimately leading to more informed decisions and increased efficiencies.
Key Strategies to Boost Productivity in Your Laundry Operations
Adopting Technology: The Key to Enhanced Performance
The integration of modern technology in laundry operations can significantly enhance efficiency and productivity. For instance, the use of digital management systems streamlines various tasks, such as scheduling, inventory management, and customer communication. As detailed in the Ultimate Guide to Laundry Operations, implementing systems like RFID for garment tracking and automated equipment can drastically reduce manual handling and improve accuracy in laundry processing.
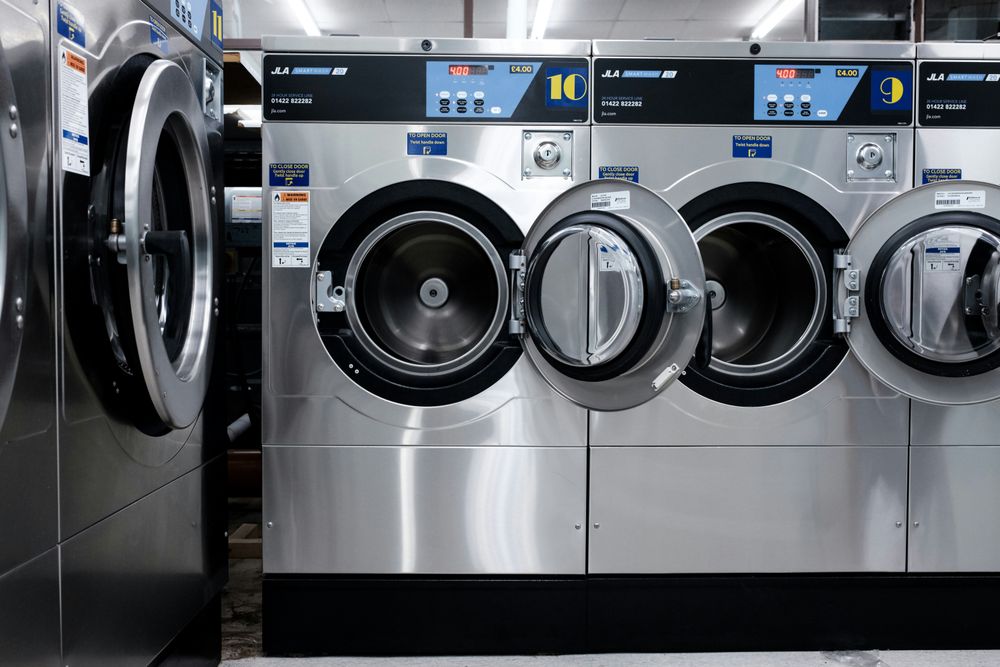
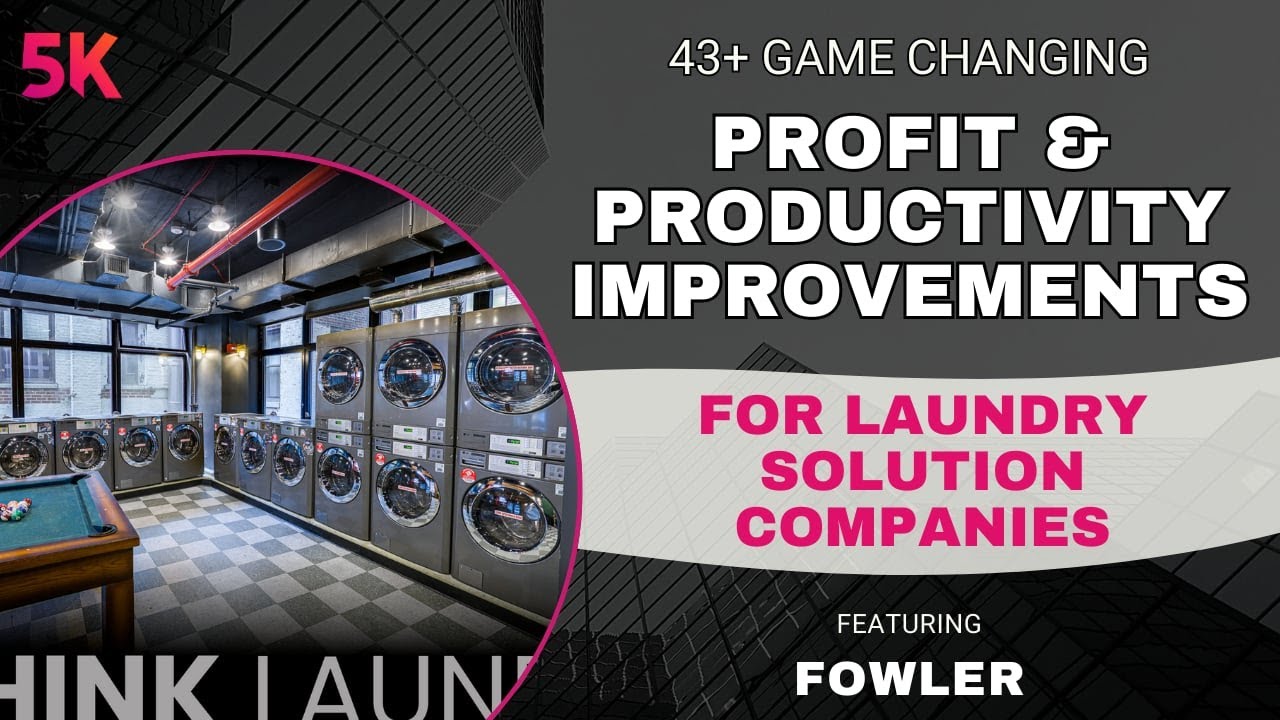
Furthermore, energy-efficient equipment can help reduce utility costs while increasing output. According to Alsco, advancements in industrial laundry technology, like automated dispensing systems for detergents, not only streamline operations but also ensure high-quality cleaning with minimal waste.
Employee Training: A Crucial Element for Productivity
Training staff on efficient operational practices cannot be overstated. Well-trained employees are more likely to adhere to safety protocols, operate equipment correctly, and maintain high service quality. Programs focusing on digital literacy and familiarization with management software, such as that discussed in American Laundry News, can vastly improve operational performance. Regular training sessions reinforce skills and promote a culture of continuous learning and improvement which is essential in maintaining operational efficiency.
Benefits of Streamlining Processes for Increased Profitability
Reducing Operational Costs through Process Optimization
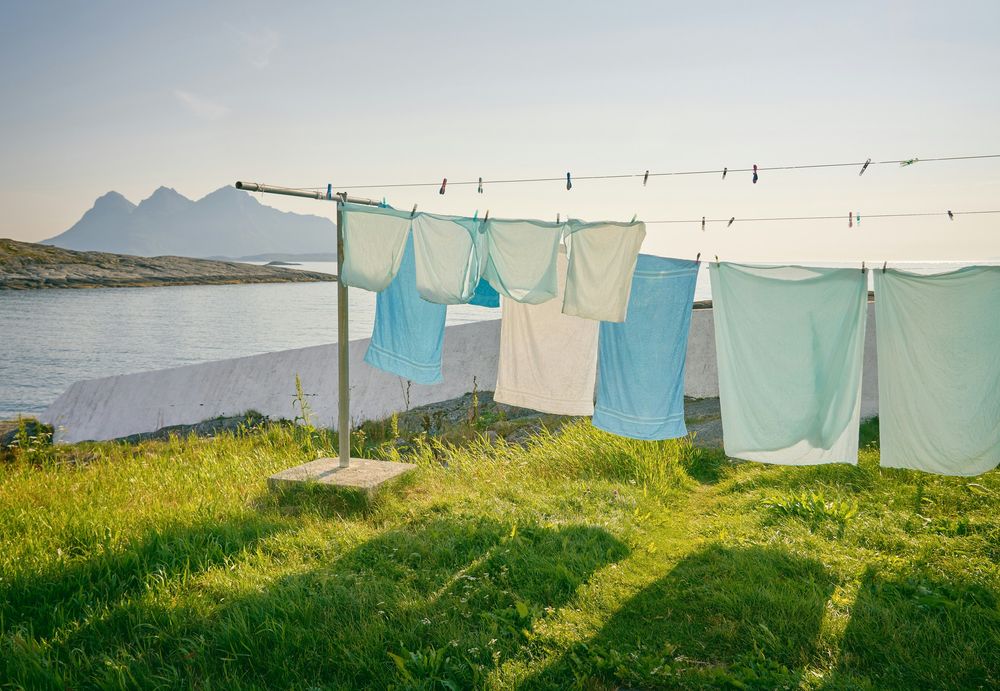
Streamlining laundry processes leads to significant cost savings, particularly through resource optimization. Implementing advanced systems helps monitor usage, as seen in modern laundromats utilizing advanced laundry technologies, which report on resource consumption and maintenance needs. This real-time data allows for better decision-making and helps reduce wasteful practices that could inflate operational costs.
An essential aspect of this is creating a customer-centric experience. A focus on service quality combined with efficiency can lure repeat business, thus maximizing profitability. Businesses that improve their processes not only save on costs but also enhance the customer experience, leading to increased loyalty and profit margins.
Creating a Customer-Centric Experience in Laundry Services
A robust customer relationship can be supported by technology that enables seamless communication, tracking orders, and managing feedback efficiently. Building trust through transparency in operations ensures that customers feel valued and appreciated, which encourages repeat transactions.
Frequently Asked Questions About Operational Efficiency in Laundry Services
What Are Common Challenges in Achieving Operational Efficiency?
Identifying potential bottlenecks is vital. Operational challenges such as equipment breakdowns, staffing issues, or delays in process flow can have major impacts on efficiency. Regular performance assessments and feedback loops, as suggested in the laundry management guide, can help identify areas that require attention. By establishing a culture focused on continuous improvement and employee engagement, laundry businesses can address these challenges effectively and foster a more efficient operational environment.
In summary, boosting operational efficiency in a laundry business involves a strategic blend of technology adoption, employee training, streamlined processes, and a focus on customer satisfaction. By addressing these elements collectively, laundry businesses can lay down a strong foundation for sustained growth and profitability.
Key Performance Indicator | Description |
---|---|
Turnaround Time | Time taken from receiving laundry to returning it. |
Equipment Utilization | Effectiveness of machines used in operations. |
Resource Consumption | Monitoring water and energy usage. |
Quality Control | Inspections and quality standards for consistent service. |
Add a comment
This will be publicly visible.
Your email address will not be published.
Your comment will be reviewed by an admin before it is published.