Understanding OSHA Compliance for Laundromat Operations
Operating a laundromat involves various responsibilities, one of the most critical being compliance with the Occupational Safety and Health Administration (OSHA) regulations. OSHA was created to ensure safe and healthful working conditions by setting and enforcing standards. For laundromat owners, understanding these regulations is essential not only for legal compliance but also for the safety of employees and customers.
What are the key OSHA regulations for laundromats?
OSHA sets forth several regulations relevant to laundromats, primarily under 29 Code of Federal Regulations (CFR) 1910, which governs general industry standards. Key regulations that laundromat owners should be aware of include:
The General Duty Clause: This fundamental requirement mandates that employers maintain a workplace free from known hazards that could cause death or serious harm.
Hazard Communication Standard: Laundromats often use various cleaning agents and chemicals that require clear labeling and access to Safety Data Sheets (SDS) to inform employees about potential hazards and safe handling procedures.
Recordkeeping Requirements: If a laundromat has 10 or more employees, it must keep a record of work-related injuries and illnesses using OSHA forms (301, 300, and 300A). This documentation must be available for review upon request.
Personal Protective Equipment (PPE) Standards: Employers must provide appropriate PPE when there is a risk of injury from chemicals or machinery.
Common compliance challenges faced by laundromat owners
Creating a culture focused on safety within laundromats not only encourages compliance with OSHA regulations but also enhances employee morale and customer satisfaction.
Laundromat owners might encounter several compliance challenges due to the nature of their operations:
Employee Training: Many owners may struggle with effectively training their staff on OSHA regulations and safety practices. Regular and updated training sessions are essential to keep employees informed.
Chemical Hazards: The presence of various chemicals used in laundry practices can lead to frequent OSHA citations if the chemical safety standards and hazard communication requirements are not met.
Recordkeeping: Keeping accurate records of safety incidents and training sessions can be cumbersome, particularly in small laundromats where staff may juggle multiple tasks.
Regulatory Updates: The changing nature of OSHA regulations can make it difficult for laundromat operators to keep up-to-date with the necessary compliance adjustments needed for their operations.
Addressing these challenges requires prioritization of safety as a core value within the laundromat business. As highlighted by Planet Laundry, creating a culture focused on safety not only encourages compliance but also enhances employee morale and customer satisfaction.
Essential Safety Practices for Laundromats
Safety practices are vital for the well-being of both employees and customers in a laundromat setting. Implementing effective safety measures can reduce hazards and improve compliance with OSHA regulations.
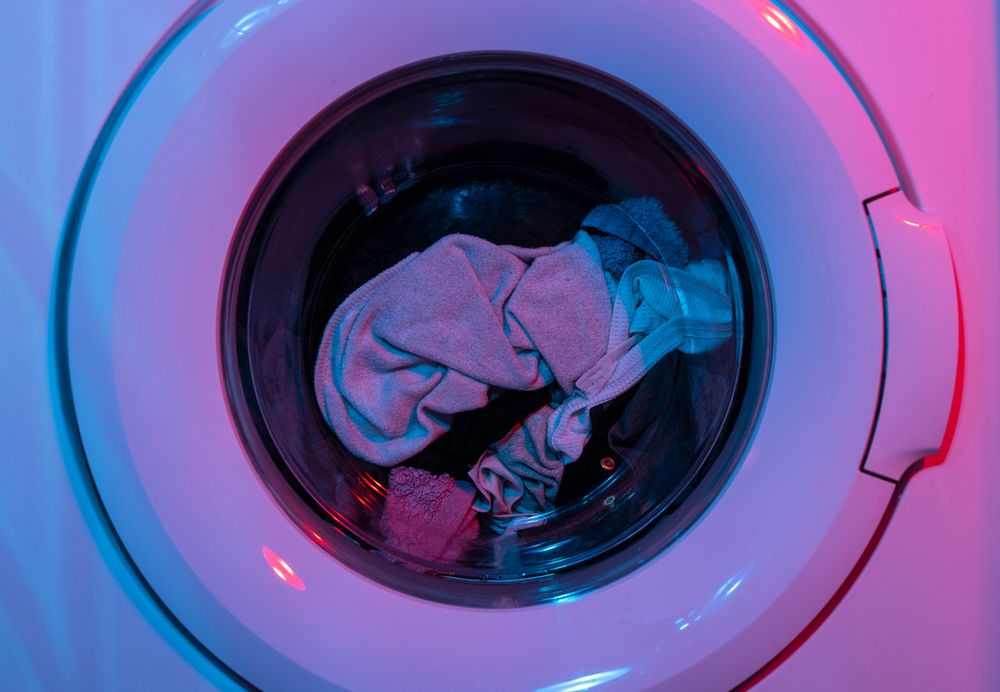
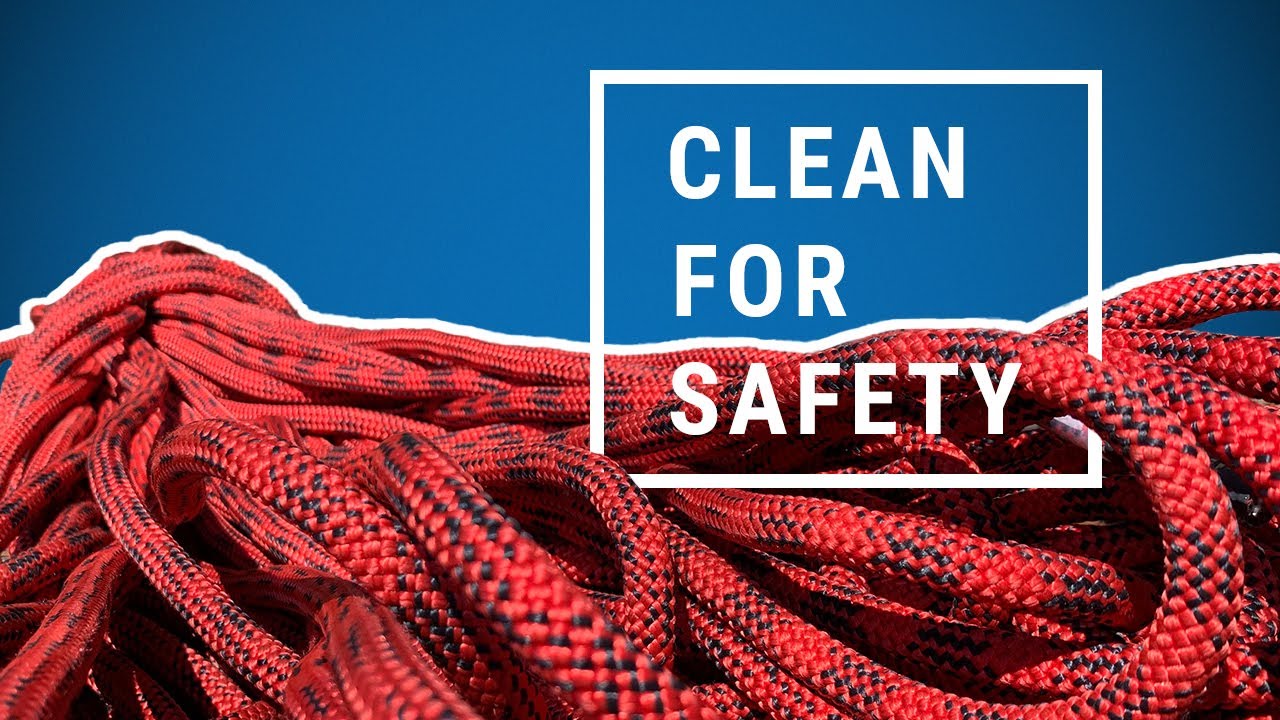
Implementing proper employee training programs
Establishing comprehensive employee training programs is crucial in ensuring that all staff members are knowledgeable about safety protocols, equipment handling, and emergency response. Training programs should cover:
Hazard Recognition: Employees need to be trained to identify potential hazards in the laundromat environment, such as wet floors or malfunctioning equipment.
Chemical Safety: Detailed instruction on how to handle, store, and dispose of hazardous materials following the Hazard Communication Standard.
Emergency Procedures: Employees should be familiar with evacuation routes, emergency contact numbers, and procedures for responding to incidents such as fires or chemical spills.
Regular training sessions are vital to reinforce knowledge and adapt to any updates in safety protocols. Creating an environment where safety is emphasized, as advocated by industry leaders, not only adheres to OSHA requirements but also cultivates a responsible workplace culture.
Creating a Safe Working Environment: Tips for Laundromat Owners
A safe working environment is essential not just for compliance with OSHA regulations but also for operational efficiency and employee retention. Here are several strategies laundromat owners can implement:
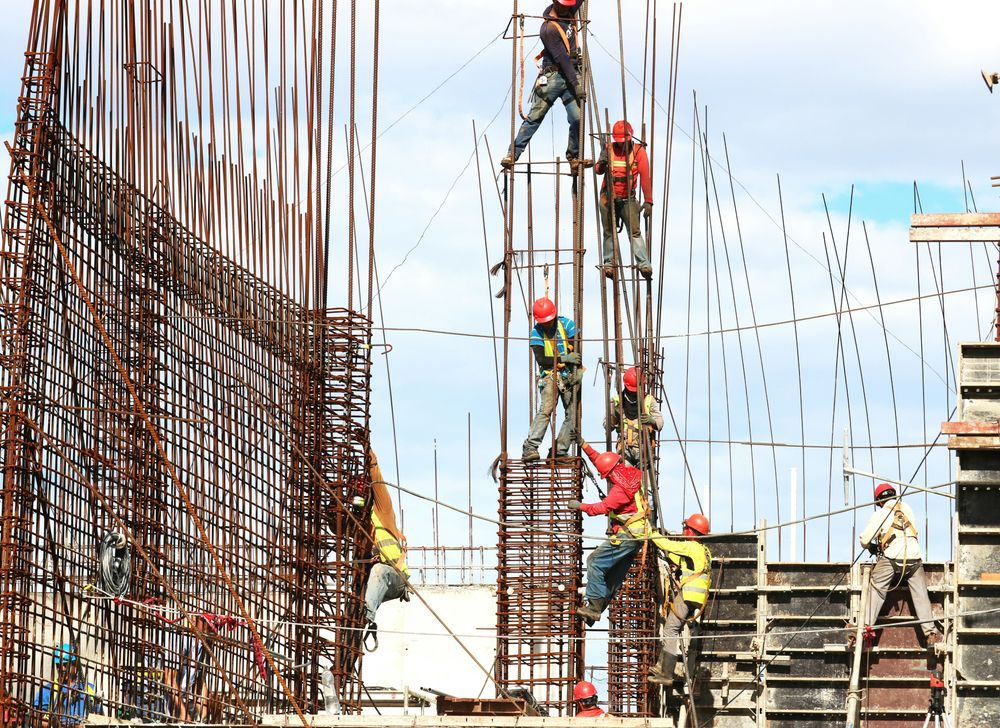
How to ensure proper ventilation in your laundromat?
Proper ventilation in a laundromat is crucial to managing heat and humidity produced by washing and drying operations. Inadequate ventilation can lead to:
Mold Growth: Excessive moisture can encourage the growth of mold and mildew, presenting health risks to employees and patrons.
Equipment Efficiency: Proper air circulation helps maintain the optimal performance of equipment, reducing maintenance issues.
Owners should consider installing exhaust fans and ensuring that dryer vents are directed outdoors, preventing heat and moisture accumulation in the facility. Regular maintenance and checks of the ventilation systems are needed to ensure compliance with local codes and standards, as outlined in the Proper Laundry Room Ventilation Guide.
Frequently Asked Questions About OSHA Compliance in Laundromats
What should a laundromat owner do if they receive an OSHA inspection?
Receiving an OSHA inspection can be stressful, but being prepared can ease the process. Here are steps laundromat owners should take:
Stay Calm and Professional: Facilitate the inspection and provide the inspector with necessary documentation, including safety records and training materials.
Know Your Rights: As an employer, you have the right to ask for identification and understand the inspection process.
Cooperate but Don't Overshare: Answer questions truthfully but avoid volunteering unnecessary information that could lead to complications or liability.
Take Notes: Document the inspector's findings and any suggestions they provide during the visit for future reference.
Understanding the inspection process can alleviate stress and help ensure prompt compliance with any recommendations made by OSHA. Being proactive about safety and compliance can significantly improve outcomes during an inspection.
By committing to OSHA compliance, laundromat owners can create a safer work environment that benefits both their employees and customers. Keeping up with regulations and implementing safety practices not only prevents injuries but also enhances the overall success of the business.
Add a comment
This will be publicly visible.
Your email address will not be published.
Your comment will be reviewed by an admin before it is published.